Thermoforming and plastic injection molding: Injection molding involves injecting molten liquid polymers into a mold at high temperature and extreme pressure. Once the mold cools, the newly formed plastic parts are released. On the other hand, thermoforming involves heating thermoforming plastic sheets and forming them to a mold’s surface.
The thermoforming Process:
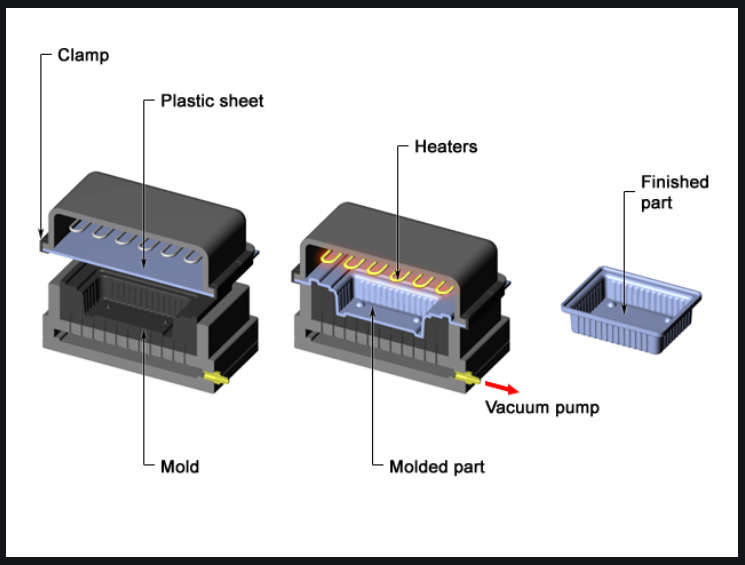
A single sheet of plastic is clamped securely in the machine. The plastic is then heated.
The plastic is placed over a mold. Molds can be either positive/male (where the plastic is formed over the mold) or negative/female (where the plastic is formed into the mould).
A vacuum draws the plastic into or against the mold.
The part is cooled and removed from the mould. Depending on the material type, water may be run through the mould to assist with the forming and cooling process. The part is removed from the mould, trimmed as necessary, and ready for shipment.
Thermoforming: A plastic processing technology, the main principle is to flatten the plastic sheet hard to soften after heating. After cooling forming, the vacuum adsorption on the mold surface is widely used in plastic packaging, lighting, advertising, decoration, and other industries.
Thermoforming packaging: the use of plastic products to produce plastic products, and equipment with the corresponding package of products in general. Blister packaging products include blister, trays, plastic boxes, and vacuum hoods, such as blisters.
The main advantages of plastic packaging are to save raw and auxiliary materials, lightweight, easy transportation, good sealing performance. In line with the requirements of environmental protection green packaging; Can pack any special-shaped products, packing without additional cushioning material; Beautiful appearance,
easy to sell, and suitable for mechanized, automated packaging. Easy to modern management, save manpower, and improve efficiency.
Thermoforming packaging equipment includes plastic molding machines, presses, sealing machines, high-frequency machines, Flap machines. Packaging the formation of packaging products can be divided into the card, suction card, double bubble shell, half bubble shell, folding bubble shell, three bubble shell.
The Injection molding process
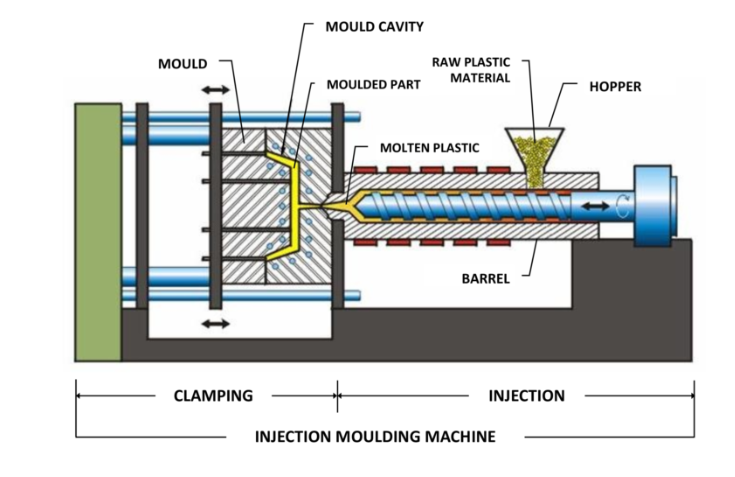
It is thermoplastic injection molding, this method is to melt the plastic material. And then injected it into the membrane cavity. Once the molten plastic enters the mold, it is cooled by the mold cavity into a certain shape.
The resulting shape is often the final product, and no additional processing is required before installation or as a finished product. Many of the details, such as the bosses, ribs, threads, can be molded in one step in injection molding operations.
The injection molding machine has two basic components: for melting and the plastic into the mold of the injection device and mold clamping device. The role of the die assembly is to:
1. The mold is closed under the pressure of the injection;
2. The article is removed from the injection device to melt the plastic before it is injected into the mold. And then the pressure and speed are controlled to inject the melt into the mold. There are two types of injection devices currently in use: screw-type pre-plasticizers or two-stage devices. And reciprocating screws. Screw-type pre-plasticizer using pre-plasticized screw (first stage) And then injected into the injection of molten plastic injection rod (second stage).
The advantages of screw pre-plasticizers are constant melt quality, high pressure and high speed, and precise
injection volume control (using mechanical thrusters at both ends of the piston stroke). These strengths are
required for transparent, thin-walled products and high production rates. Disadvantages include non-uniform
residence times (leading to material degradation), higher equipment costs, and maintenance costs.
The most common reciprocating screw injection device does not require a plunger to melt and inject the plastic.