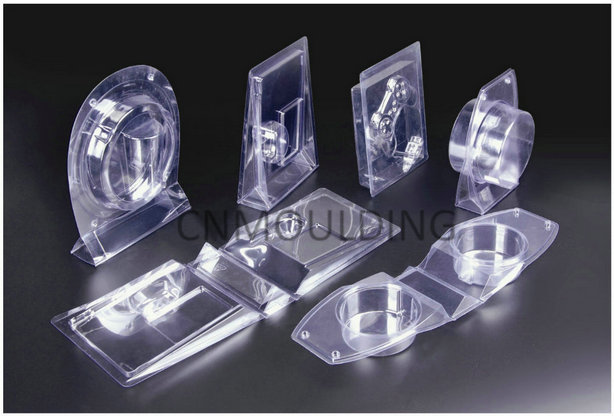
Thermoforming mold
The Thermoforming molds include plaster molds, electroplated copper molds, and aluminum molds.
Gypsum mold: plaster molding in the semi-wet state, and then drying mold, plaster mold low cost, easy to
modify, but the plaster mold precision is not high enough. The surface is not smooth and fragile is not durable, so it is often used to fight. To do the electroplating of copper mold or some of the requirements of small-batch production of plastic mold.
Aluminum mold: with aluminum ingots through the machinery (lathes, milling machines, CNC, etc.) from
processing. Aluminum mold high precision, smooth surface, and durability. But the price is very expensive, aluminum mold is generally used in a high precision copper mold not reach the blister products.
Electroplated copper mold: Plaster mold made of samples, the plating layer of the copper shell is the electroplating copper mold. The cost of relatively high plaster mold, but much cheaper than aluminum mold. Because of its smooth and durable surface, low cost, electroplating Copper mold is the most commonly used plastic mold.
The choice of thermoforming material
Thermoforming packaging products include bubble shells, trays, plastic boxes, as well as: vacuum cover, thermoforming, and so on.
Thermoforming products are only plastic sheet material, the film thickness is generally not more than 1.5MM. thermoforming material commonly used sheet: PVC, PET, PP, PS and on this basis, flocking sheet, gold-plated sheet, and anti-static sheet.
PVC: the most commonly used plastic material, soft, tough, good plasticity. It can be made transparent and a variety of colors, commonly used transparent PVC packaging electronics, cosmetics, toys, gifts, and other products.
PET (A-PET): hard, good toughness, high strength, bright surface, environmentally friendly non-toxic, transparent, and a variety of colors of the sheet. Disadvantages of PET high-frequency heat more difficult, the price is much more expensive than PVC. This material is often required to replace high-end and environmentally friendly products, PVC
PS: small density (light), environmental non-toxic, plasticity is very good, toughness is not easy to brittle, can not be made of transparent material, it can only be made at the end of care plastic, because of its easy to crack,
PP: the material is particularly soft, tough, environmentally friendly non-toxic, high temperature, often made of food containers or other high-temperature packaging products; but its poor plasticity, processing difficulties, poor surface gloss, and the processing of color change shallow.
PET-G: physical properties with the A-PET almost, but high-frequency heat, the price is more expensive than A-PET 80%
The plastic product price determinants
Thermoforming = unit material cost of materials + energy + labor + transport + profits
Energy consumption: thermoforming is through thermal processing, power consumption relative to other industries larger, roughly for the material cost of 8%.
Artificial: thermoforming mainly by machine production, less artificial, roughly 10% of the cost of materials,
Transportation: According to the customer from the factory and distance,
Profit: Plastic factory net profit is generally low, 12% -20%, depending on the payment period, 30 days checkout is 14%
Material cost: The material cost of the product is relatively complicated. Before the calculation, the following data should be clarified:
Raw material price: according to the use of the product, to determine what kind of material and grade of material. To find the lowest price of these material suppliers.
Film Thickness: Extending The product must be made of thick film, according to the shape of the various parts of the thickness and shape.
The number of typesetting: according to the size and shape of the product, the number of molds can be calculated in a version. The density will reduce the quality of products, thinning will increase the material loss, so that the cost of material loss rate: The main factor is the product shape, The number, and size of the chassis fit with the degree of plastic. The shape of the more Founder, the greater the output, the smaller the loss rate.