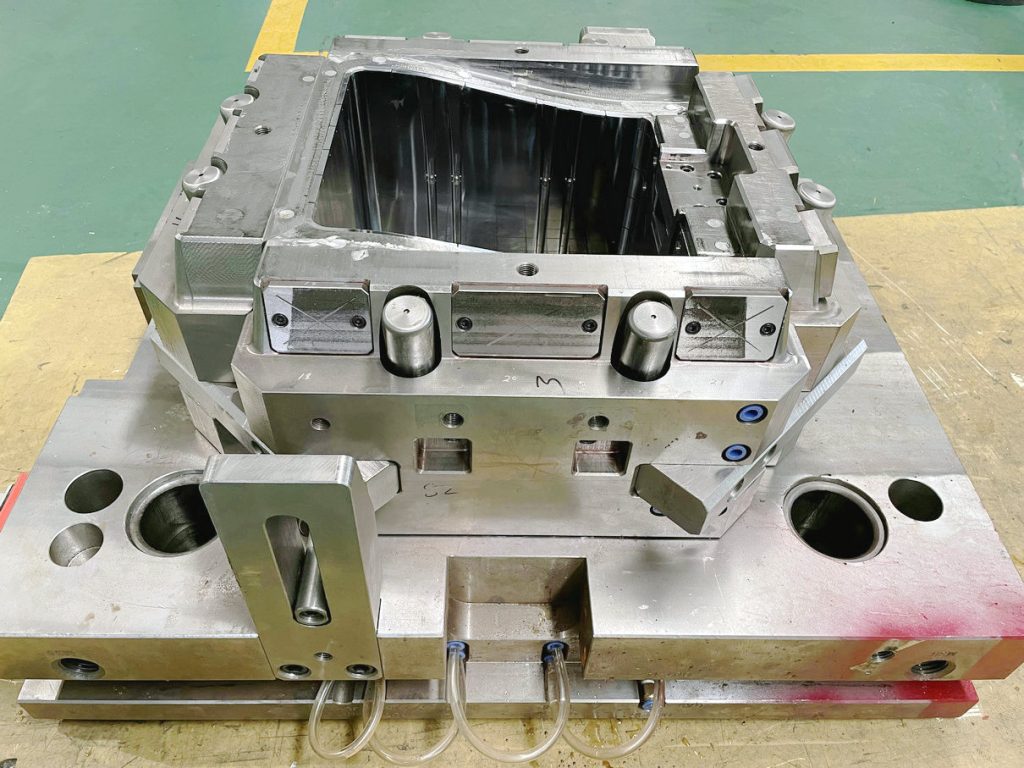
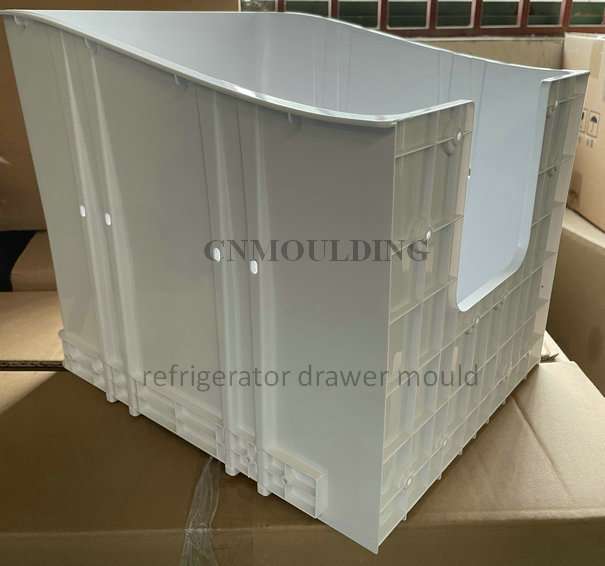
The picture file is the refrigerator drawer injection mold, which uses a single-mouth open hot runner to feed the product directly. The front mold is left in its original form, and the back mold is inlaid with mold cores. The big row on one side meets the big inclined roof, and the small row on both sides is structured. Cooling water is passed through both the row position and the inclined roof, and the top block is used for ejection.
Features
- One-point needle valve in the hot runner, with beautiful breakpoints;
- GPPS is transparent, highly non-toxic, fully automatic production, no bubbles, no cracks in appearance;
- Food-grade non-toxic materials, environmental protection, no cracks;
Refrigerator drawer molds generally use PP or PC, which have better permeability and higher product surface requirements, which are high-gloss molds. So how to make this refrigerator drawer mold?
The high-gloss mold is controlled by the mold temperature machine to control the mold temperature, and the hot runner, solenoid valve, and time relay control the time-sharing glue feeding, so as to produce high-end products with a bright appearance, no shrinkage, no welding marks, and other defects.
High-gloss molds generally have the following characteristics:
- The molding temperature is relatively high (usually around 80-90 degrees)
Pressure-holding molding at a higher mold temperature is beneficial to eliminate defects such as weld marks, flow marks, and product internal stress. Therefore, the mold needs to be heated during work. In order to prevent heat loss, a resin insulation board is usually added to the fixed mold side. - The surface of the cavity is extremely bright (generally mirror level 2 or higher)
The products produced by the high-gloss mold can be directly used for installation without any surface treatment. Therefore, it has high requirements for mold steel and plastic materials. - The hot runner system has more hot nozzles (usually 6-8 nozzles, sometimes more)
Each hot nozzle must be equipped with a sealing needle and an independent air passage, which is individually controlled by solenoid valves and time relays to realize time-sharing glue feeding, so as to achieve the purpose of controlling or even eliminating weld marks.
Key Points of Refrigerator Drawer Mould Design
1, Refrigerator drawer mold requirements for product structure
Refrigerator drawer molds have strict requirements on product structure. As we all know, the brighter the product, the more sensitive it is to the effect of light refraction, and a slight defect on the surface will soon be found. Therefore, the first thing to solve is the shrinkage problem. According to empirical statistics, the thickness of the ribs of general products does not exceed 0.6 times the thickness of the main glue position, and it will not shrink, or the shrinkage is small and difficult to be found, so it can be ignored. But for refrigerator drawer molds, this requirement is far from enough. It is necessary to reduce the thickness of the product ribs to no more than 0.4 times the thickness of the main body glue. For the screw posts, special treatment must be done.
2, Hot runner system of refrigerator drawer mould
The hot runner system is very important for the refrigerator drawer mold. Whether or not a product without weld marks can be injected, the quality of the hot runner and the adjustment of the machine are the decisive factors. The characteristics of the refrigerator drawer mold runner system: the hot nozzle of the refrigerator drawer mold must have a sealing needle, and each hot nozzle must have an independent air channel (multiple air channels are not allowed to be connected in series), so that the solenoid valve can be passed And time relay to individually control the glue feeding time and amount of each hot nozzle, making necessary preparations for the injection molding machine.
3, Cooling and heating system of refrigerator drawer mould.
When the plastic material is injected into the mold cavity, within a reasonable temperature range, the higher the surface temperature of the mold cavity, the better the surface quality of the product, and the smaller the internal stress of the product. Therefore, in order to obtain a good product surface quality, it is a good way to increase the surface temperature of the cavity (however, increasing the mold temperature will reduce the injection efficiency, which requires comprehensive consideration). Generally, the refrigerator drawer mold is heated by a mold temperature machine during injection molding, so that the plastic is held in a high-temperature state in the mold, and the temperature is maintained, so as to eliminate defects such as flow marks and weld marks and achieve a mirror effect.
The water channel of the refrigerator drawer mold must not only be uniform but also must be sufficient, so that the required temperature can be easily reached by the mold temperature machine. At the same time, the use of an extended water pipe to directly transport the mold core without using a sealing ring can prevent the mold from working under high temperature for a long time, causing the sealing ring to age, and can also reduce the maintenance cost of many molds. It is worth mentioning that the water pipe of the refrigerator drawer mold must use a high-temperature-resistant oil pipe to prevent the water pipe from bursting under high temperature and high pressure.