Plastic Parts Flash Solution: A Comprehensive Guide
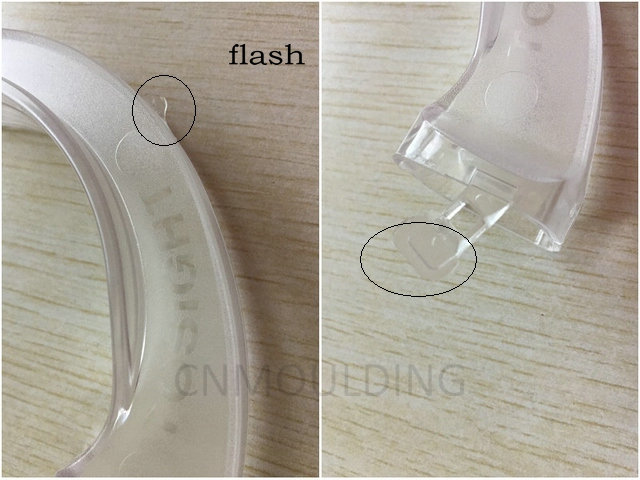
Plastic parts flash is a common problem in the injection molding process. It refers to the excess material that protrudes from the molded part due to the presence of gaps or misalignment between the mold halves. This flash not only affects the aesthetics of the finished product but also compromises its functionality. Fortunately, there are several solutions to this problem, and in this blog post, we will discuss them in detail.
Optimize the Mold Design
The first step in preventing plastic parts flash is to optimize the mold design. This includes ensuring that the mold halves are aligned correctly and that there are no gaps or misalignments. The use of high-quality materials and precision machining techniques can also help to reduce the occurrence of flash.
Adjust the Injection Molding Process
Another solution to plastic parts flash is to adjust the injection molding process. This includes optimizing the injection speed, pressure, and temperature to ensure that the plastic material flows smoothly and fills all the cavities in the mold. The use of injection molding simulation software can help to identify potential issues in the process and optimize it accordingly.
Use Mold Release Agents
Mold release agents can also be used to prevent plastic parts flash. These agents are applied to the mold surface before injection molding, and they help to reduce friction between the mold and the plastic material. This, in turn, reduces the occurrence of flash and improves the overall quality of the finished product.
Implement Post-Molding Operations
Post-molding operations such as trimming, sanding, and polishing can also be used to remove plastic parts flash. These operations are carried out after the injection molding process and involve removing the excess material using specialized tools and techniques. However, this solution is time-consuming and can increase the overall production cost.
Use Automated Deflashing Equipment
Automated deflashing equipment is another solution to plastic parts flash. This equipment uses specialized tools and techniques to remove the excess material from the molded parts automatically. This solution is faster and more efficient than manual trimming and can significantly reduce the overall production cost.
Reference
1, Should be paid attention to, for the mold and excessive clamping pressure also can produce flash, parting surface, between the clip into the foreign body damage both mold and produces the burrs.
2, Injection mold material often use S50C JJS (Japan standard domestic 50 # steel) using HRC30 hardening of the special steel in advance, it is difficult to produce burrs in parting surface
Conclusion
Plastic parts flash is a common problem in the injection molding process, but it can be prevented using various solutions such as optimizing the mold design, adjusting the injection molding process, using mold release agents, implementing post-molding operations, and using automated deflashing equipment. Each solution has its advantages and disadvantages, and the choice of solution will depend on the specific requirements of the product and the production process. By implementing these solutions, manufacturers can improve the quality of their products and increase their competitiveness in the market.