The reasons for sink mark in plastic products are as follows:
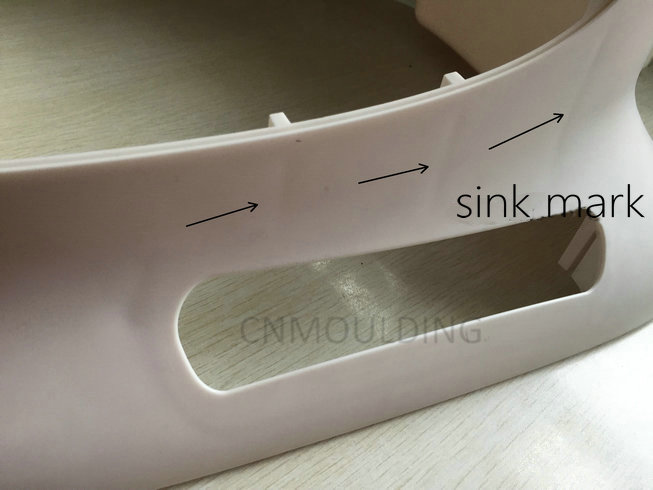
Reasons for injection molding sink mark
Sink marks in injection molding are common defects that occur when the surface of a molded part shrinks and creates a depression or dimple. This typically happens because the inner part of the material cools and shrinks faster than the outer surface, pulling the surface inward. Sink marks are most noticeable on thicker sections of the part or near ribs, bosses, or other features that create variations in wall thickness.
Causes of Sink Marks:
- Insufficient Cooling Time:
- If the cooling time is too short, the outer surface solidifies while the inner material is still cooling and shrinking, causing sink marks.
- Inadequate Holding Pressure or Time:
- Holding pressure helps pack additional material into the mold to compensate for shrinkage. If the pressure or time is insufficient, the material shrinks excessively, leading to sink marks.
- Excessive Wall Thickness:
- Thicker sections cool more slowly, increasing the likelihood of shrinkage and sink marks.
- High Material Shrinkage Rate:
- Some materials, such as semi-crystalline plastics (e.g., polypropylene or nylon), have higher shrinkage rates, making them more prone to sink marks.
- Improper Gate Location or Size:
- If the gate is too small or poorly located, it can restrict the flow of material, preventing adequate packing and leading to sink marks.
- High Melt Temperature:
- Excessive melt temperature can increase material shrinkage as it cools, contributing to sink marks.
How to Prevent Sink Marks:
- Optimize Wall Thickness:
- Design parts with uniform wall thickness to ensure even cooling. If thick sections are unavoidable, use coring or ribbing to reduce material volume.
- Increase Holding Pressure and Time:
- Apply sufficient holding pressure and extend the holding time to pack more material into the mold and compensate for shrinkage.
- Adjust Cooling Time:
- Ensure adequate cooling time to allow the entire part to solidify uniformly.
- Use Low-Shrinkage Materials:
- Select materials with lower shrinkage rates, such as amorphous plastics (e.g., ABS, PC) or filled resins.
- Optimize Gate Design:
- Use larger gates or position them near thicker sections to ensure proper material flow and packing.
- Control Melt Temperature:
- Avoid excessively high melt temperatures to minimize shrinkage.
- Add Mold Features:
- Incorporate mold features like gas vents or cooling channels to improve cooling efficiency and reduce shrinkage.
Corrective Actions for Existing Sink Marks:
- Increase holding pressure and time.
- Reduce melt temperature.
- Extend cooling time.
- Modify part design to reduce wall thickness or add coring.
- Adjust gate size or location.
By addressing these factors, you can minimize or eliminate sink marks and improve the quality of injection-molded parts.
Injection molding sink Mark– its causes and solutions
Injection Molding Sink Marks: Causes, Prevention, and Remedies
Injection molding is an incredibly versatile manufacturing process that can produce a wide range of plastic components. However, one common issue that can arise during the injection molding process is the appearance of sink marks on the surface of the molded parts. Sink marks can detract from the aesthetic quality of the finished product and may even compromise its structural integrity. In this post, we’ll explore the causes of injection molding sink marks and discuss some prevention and remediation strategies.
What are Injection Molding Sink Marks?
Injection molding sink marks are depressions or indentations that appear on the surface of a molded part. These marks can occur when the surface of a part cools and solidifies before the underlying material has completely filled out. This can result in a depression or indentation on the surface of the part, which is known as a sink mark.
Causes of Injection Molding Sink Marks
There are several factors that can contribute to the formation of sink marks during the injection molding process. One common cause is inadequate packing pressure, which can result in incomplete filling of the mold cavity. This can create voids or air pockets in the material, which can cause sink marks to form as the material cools.
Another factor that can contribute to sink mark formation is insufficient cooling time. If a part is ejected from the mold too soon, it may not have had sufficient time to cool and solidify, which can cause sink marks to form as the material continues to shrink.
Prevention Strategies
One of the most effective ways to prevent injection molding sink marks is to optimize the injection molding process itself. This may involve adjusting the packing pressure, cooling time, or other process parameters to ensure that the material fills out the mold cavity completely and cools evenly.
Another effective prevention strategy is to modify the design of the part itself. By adding ribs or other structural features to the part, it may be possible to reduce the amount of material required to fill out the mold cavity, which can help to prevent sink marks from forming.
Remediation Strategies
If sink marks do appear on a molded part, there are several remediation strategies that can be employed. One common approach is to use a filler material to fill in the depression or indentation. This can help to restore the surface of the part to its original shape and smoothness.
Another remediation strategy is to use heat or pressure to “heal” the sink mark. By applying heat or pressure to the affected area, it may be possible to cause the material to flow back into the depression or indentation, effectively eliminating the sink mark.
Conclusion
Injection molding sink marks can be a frustrating and costly problem for manufacturers. However, by understanding the causes of sink marks and implementing effective prevention and remediation strategies, it is possible to minimize their impact and produce high-quality molded parts. By optimizing the injection molding process, modifying part designs, and employing remediation techniques when necessary, manufacturers can ensure that their products meet the highest standards of quality and performance.
In addition, to the sink mark, the production process will encounter shrinkage, then you need a different solution