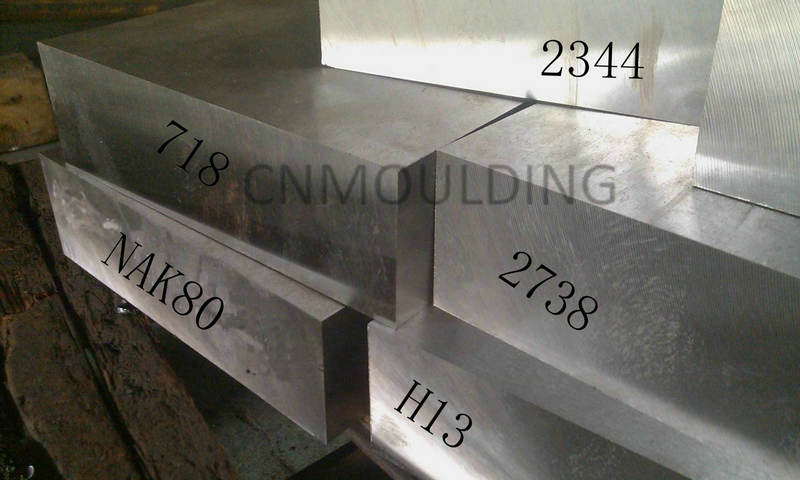
Injection Mold Steel: The Key to High-Quality and Durable Molded Products
Injection mold steel is a critical material used in the manufacturing of molds for plastic injection molding. The choice of mold steel significantly impacts the quality, durability, and performance of the molds, which in turn affects the efficiency and cost-effectiveness of the injection molding process. Below is an overview of injection mold steel, including its properties, types, selection criteria, and applications.
Properties of Injection Mold Steel
Injection mold steel must possess specific properties to withstand the demanding conditions of the injection molding process. Key properties include:
- High Hardness
- Ensures the mold can resist wear and deformation during repeated use.
- Typically measured on the Rockwell hardness scale (HRC).
- Excellent Machinability
- Allows for precise and efficient machining of complex mold geometries.
- Good Thermal Conductivity
- Helps dissipate heat quickly, reducing cycle times and preventing overheating.
- High Corrosion Resistance
- Essential for molds used with corrosive materials or in humid environments.
- Toughness and Impact Resistance
- Prevents cracking or chipping under high-pressure conditions.
- Dimensional Stability
- Maintains shape and accuracy under varying temperatures and pressures.
- Polishing and Surface Finish
- Enables the production of high-quality, smooth surfaces on molded parts.
Types of Injection Mold Steel
Injection mold steels are categorized based on their composition, hardness, and application. Common types include:
- Pre-Hardened Steels
- Examples: P20, 718, NAK80
- Characteristics: Pre-hardened to a specific hardness (e.g., 28-36 HRC), reducing the need for additional heat treatment.
- Applications: General-purpose molds, low to medium production runs.
- Tool Steels
- Examples: H13, S7, D2
- Characteristics: High hardness and wear resistance, often requiring heat treatment.
- Applications: High-volume production, molds for abrasive materials.
- Stainless Steels
- Examples: 420, 440C
- Characteristics: Excellent corrosion resistance and polishability.
- Applications: Molds for medical, food, and cosmetic industries.
- High-Speed Steels
- Examples: M2, M42
- Characteristics: Exceptional hardness and heat resistance.
- Applications: Molds for high-temperature plastics or extreme conditions.
- Maraging Steels
- Characteristics: Ultra-high strength and toughness, with good dimensional stability.
- Applications: Precision molds for complex parts.
Selection Criteria for Injection Mold Steel
Choosing the right mold steel depends on several factors:
- Production Volume
- High-volume production requires harder, more wear-resistant steels (e.g., H13, D2).
- Low to medium volumes can use pre-hardened steels (e.g., P20, 718).
- Material Being Molded
- Abrasive materials (e.g., glass-filled plastics) require high-wear-resistant steels.
- Corrosive materials (e.g., PVC) require corrosion-resistant steels (e.g., 420 stainless steel).
- Part Complexity and Surface Finish
- Complex geometries and high-gloss finishes require steels with excellent polishability (e.g., NAK80, 420).
- Mold Lifespan
- Longer lifespans require tougher, more durable steels.
- Cost Considerations
- Balance performance requirements with budget constraints.
Heat Treatment and Surface Treatments
To enhance the performance of injection mold steels, various treatments can be applied:
- Heat Treatment
- Processes like quenching and tempering improve hardness and toughness.
- Surface Hardening
- Techniques like nitriding or carburizing increase surface hardness and wear resistance.
- Coatings
- Coatings such as TiN (Titanium Nitride) or DLC (Diamond-Like Carbon) reduce friction and improve corrosion resistance.
Conclusion
Injection mold steel is a vital component in the plastic injection molding process, directly influencing mold performance, part quality, and production efficiency. By selecting the appropriate steel type and applying suitable treatments, manufacturers can optimize their molds for specific applications, ensuring durability, precision, and cost-effectiveness. As the demand for high-quality plastic parts continues to grow, the role of advanced mold steels will remain critical in meeting industry needs.