The elbow mold is used to deal with the position that cannot be demolded on the parting surface of the product. It belongs to the “undercut processing system” and is a structure of the mold.
Elbow mold definition: is called angle pin core pulling mold. A mechanism that guarantees the smooth demolding of the product is also called a slider. For example, there is a hole on the side of a plastic part. After the mold is opened, if the core of the hole is not removed, the product cannot be ejected. At this time, the structure of the mold should adopt the structure of the slider. The core of the hole is made movable. The inclined guidepost is matched with the fixed mold. The slider moves with the mold opening or closing. This kind of movement is called core pulling.
1. For mold blanks smaller than 2020, pry pits are required between the A and B plates. Mold blanks larger than 2020 must be pry pits between all templates including thimble plates.
2. The mold base guide post and guide sleeve should be processed with exhaust grooves to prevent the guide post and guide sleeve from straining.
3. There must be no sharp corners on the mold and chamfering is required. Except where specified.
4. The inner mold and mold parts shall not be welded without consent.
5. Exhaust grooves must be opened at appropriate positions on the periphery of mold products.
6. Avoid using a grinder to polish the mold as much as possible. If you must use a grinder to process, you must use the oilstone to save the light. (especially the parting surface)
7. The surface treatment of the inner mold surface must be performed in accordance with the BOM or other officially notified technical requirements. The processing lines (wire cutting, milling machine, CNC gong machine, spark machine) on the non-adhesive plane should also use the oilstone to save the light.
8. All inner mold materials and mold blank grade requirements must be purchased according to the order or the technical requirements formally confirmed during the design review process. Material certification must be provided, if it is a hard mold, a heat treatment report must be provided.
Elbow mold design
The elbow products are shown in the figure below, with a greater degree of bending
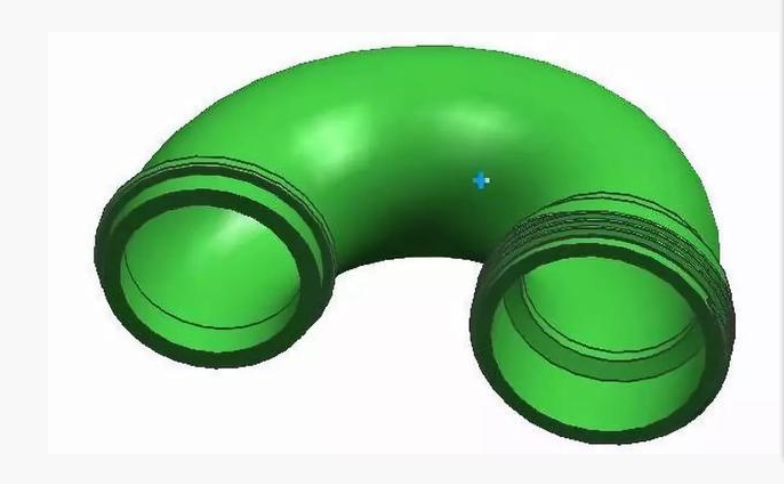
Since the arc core pulling degree is relatively large, the oil cylinder is required to pull the core, as shown in the figure below
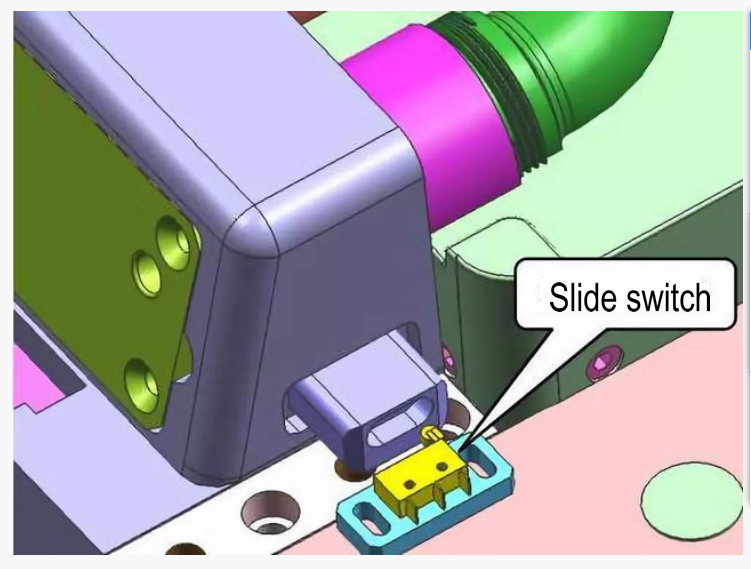
For arc core pulling, you need to divide the slider insert into several pieces, and pull the core along the arc of the product during core pulling, as shown in the figure below
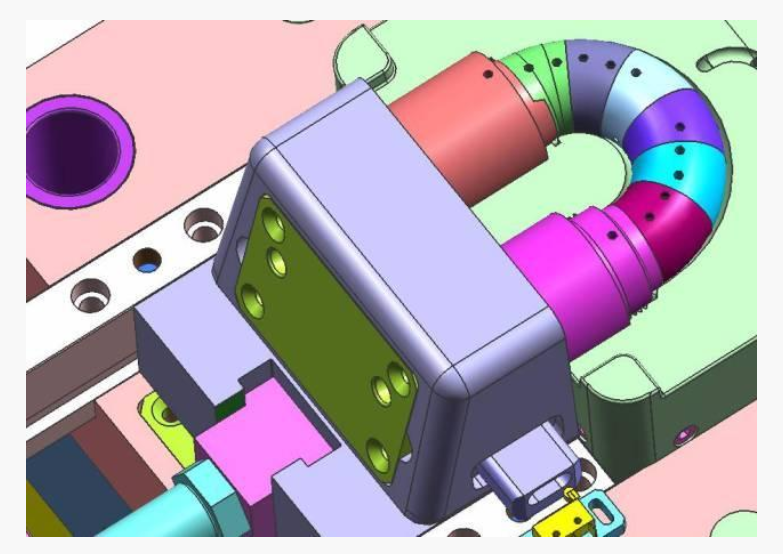
The slider inserts are connected by a key and positioned by a pin, as shown in the figure below.
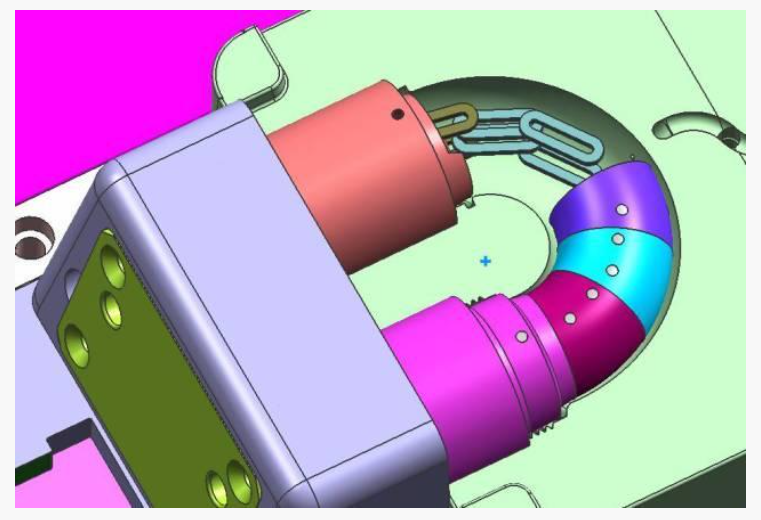
The position of the key in the slider insert must be avoided to avoid interference between the key and the slider insert. when the arc core is pulled, as shown in the figure below.
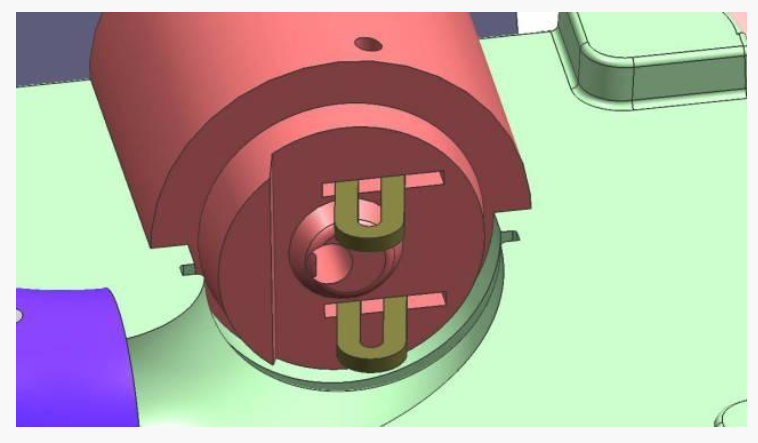
Positioning must be done between the slider inserts. Facilitate smooth mold clamping, It Will not be misaligned, as shown in the figure below.
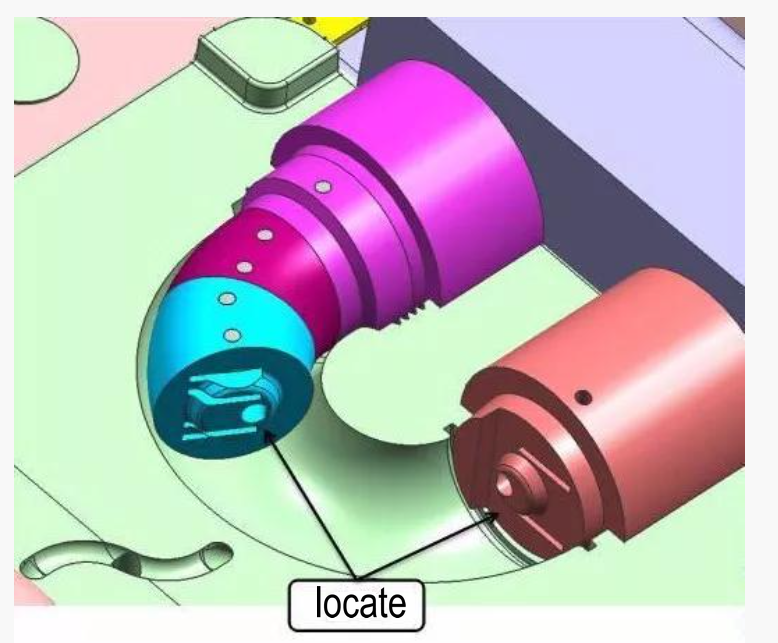