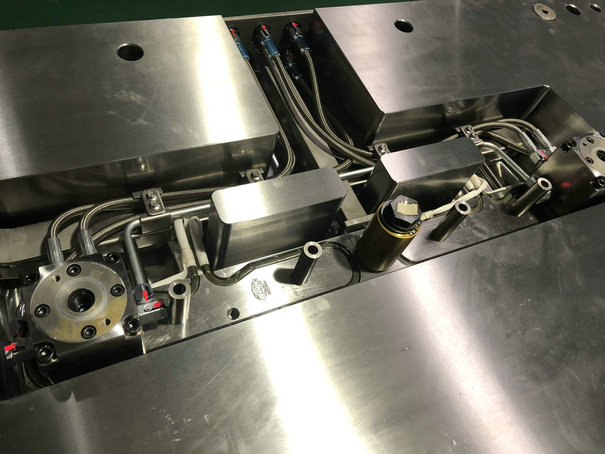
Injection molding is a widely used manufacturing process in various industries. It involves injecting molten material into a mold cavity to create a desired shape. One of the key considerations in injection molding is whether or not to use a hot runner system.
A hot runner system is a set of heated components that deliver molten material to the mold cavity. It consists of a manifold, nozzles, and heaters that keep the material hot and flowing. The purpose of a hot runner system is to eliminate waste and improve efficiency. By keeping the material hot and in a constant flow, there is less material waste and shorter cycle times.
However, not all injection molds require a hot runner system. The decision to use a hot runner system depends on several factors, including the size and complexity of the part being molded, the material being used, and the production volume.
For small parts with simple designs, a hot runner system may not be necessary. Cold runner systems, which use unheated channels to deliver the material, may be sufficient. Cold runner systems are generally less expensive and easier to maintain than hot runner systems.
For larger parts with complex designs, a hot runner system may be necessary to ensure proper filling of the mold cavity. Hot runner systems can also help prevent defects such as warping, sink marks, and flow lines.
The material being used also plays a role in the decision to use a hot runner system. Certain materials, such as thermoset plastics, may require a hot runner system to prevent premature curing or solidification.
Finally, the production volume must be considered when deciding whether or not to use a hot runner system. Hot runner systems are generally more expensive to purchase and maintain than cold runner systems. If the production volume is low, it may not be cost-effective to use a hot runner system.
In conclusion, not all injection molds require a hot runner system. The decision to use a hot runner system depends on several factors including the size and complexity of the part being molded, the material being used, and the production volume. It is important to carefully consider these factors when deciding on the best injection molding process for your specific application.