Cost Comparisons
Plastics are now very diversified manufacturing, consumer choice both in terms of appearance or performance,
there are more requirements. Below are explanations for three of the most common techniques, as well as how
each compares in cost. Keep in mind that costs vary by project and that some products require a combination
of techniques.
Plastic Injection Molding coat:
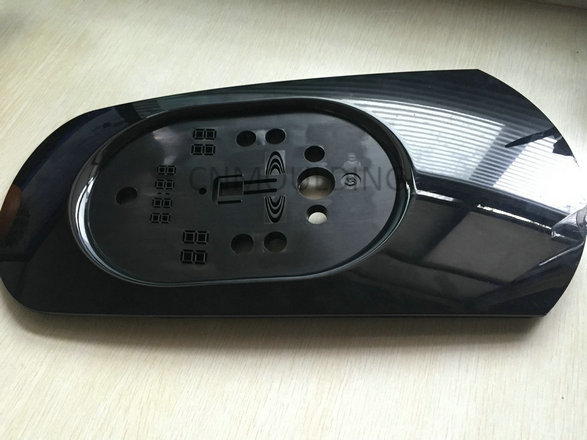
Injection molding is common processing, which is a method of molding and injection molding. The advantage
injection molding method is the production at high speed. The high-efficiency operation can be automated, color
varieties. Shapes can be from simple to complex, size can be big to small. And precise product size, product
upgrading is easy. It can become a complex shape part, injection molding suitable for mass production. And
field molding the shape of complex products. At a certain temperature, stirred by the screw completely molten plastic material, with high pressure, into the mold cavity. After cooled and solidified to obtain a molded product approach. This method is suitable
for the mass production of parts of complex shapes. It is one of the important processing methods.
How does the cost compare: In general, this process is comparatively complex. As it requires a specific mold to
be made. For that reason, it can cost more.
Rapid prototyping:
Is molten plastic injection molding machine in a plunger or a screw thrust into the mold, after the cooling
process of obtaining products? After heating the plastic injection molding machine plasticizing barrel, plunger, or reciprocating screw injection into the closed mold cavity in the plastic processing method of forming articles.
This method can process complex shapes, sizes, accuracy, or inserts of products, with high production efficiency.
For most thermoplastics and some thermosetting plastics (such as Bakelite), this method can be processed.
Materials for injection molding must have good liquidity to fill the mold cavity to obtain a product.

Thermoforming:
The thermoplastic resin sheet is processed into various articles of a more specific method of plastic processing.
The sheet caught in the frame is heated to soften the state. The external force, is firmly against the molding surface, in
order to obtain the profile of a similar shape. After cooling stereotypes, Serve the finished product. This procedure
is also used in rubber processing. In recent years, thermoforming has made new progress. For example, from an extruded sheet
thermoforming to continuous production technology.

In the market, more and more thermoformed products. Such as cups, plates, food dishes, toys, and headgear. As well as automotive parts, building trim, and chemical equipment. Thermoforming and injection molding comparison, with high efficiency, low investment and can create a larger surface area of the product advantages. For thermoforming plastic mainly polystyrene, polyvinyl chloride, and polyolefin (e.g. polyethylene, polypropylene). Polyacrylates such as poly (methyl methacrylate) and cellulose (such as cellulose nitrate, cellulose acetate, etc.) plastics. But also for engineering plastics (such as ABS resin, and polycarbonate). There are several thermoforming processes, but basically, in a vacuum, pneumatic or mechanical pressure are three ways to be based on a combination of improvements made. By its nature, this type of plastic manufacturing is simpler than the one described above and is generally less expensive.
How does the cost compare: On its own, plastic injection molding is less expensive. However, you must consider
that injection molding is often part of a larger process, in which case expenses can ultimately be higher.