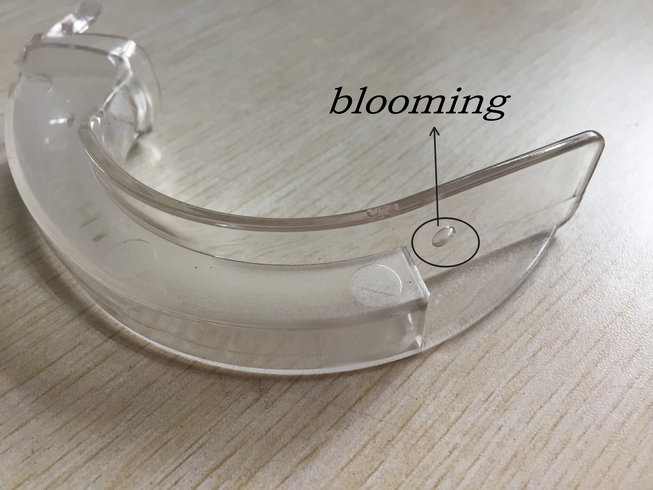
Causes of blooming in Injection Molding Products
Plastic in the filling process by gas interference often appears on the product surface in silver streaks, or tiny bubbles or thick bubbles within the product. The main source of these gases is the moisture content of raw materials or volatile substances or lubricants in excess. it may be the material temperature is too high plastic heated for a long time, degradation occurs and produce degradation gas.
1, Equipment:
The nozzle hole is too small, and the material in the nozzle salivation or drawing. Barrel or nozzle with obstacles or burrs, high-speed material flow through the friction heat decomposition.
2, Mold:
(1) Due to design defects, such as gate position is not good, the gate being too small, and more gates arranged asymmetry. The flow channel is small, the mold cooling system is unreasonable to the mold temperature difference is too large Resulting in melt flow in the mold cavity is not continuous, blocking the air channel.
(2) The lack of the necessary part of the mold exhaust vents or exhaust channels is inadequate, blocked in a poor location, and no inserts. Thimble and the like processing gap exhaust, resulting in the air cavity can not enter the plastic While leaving.
(3) Mold surface roughness is poor, with large friction resistance, resulting in local hot spots, so that through the decomposition of the plastic.
3, Technology:
(1) Material temperature is too high, resulting in decomposition. Cylinder temperature is too high or heating disorders should be paragraph by paragraph to reduce barrel temperature. The feed section temperature is too high, so that part of the plastic melt prematurely filling the groove. The air can not be discharged from the charging port.
(2) Injection pressure is small, holding pressure time is short, so that they melt and the cavity surface is not dense paste.
(3) The injection speed is too fast, so that the molten plastic by the large shear and decomposition, resulting in decomposition of gas; injection speed is too slow, can not be filled with cavities caused by insufficient surface density of products produce silver grain.
(4) Insufficient material, feeding buffer is too large, too low temperature or mold temperature will affect the melt flow and molding pressure, resulting in air blooming.
(5) With a multi-stage injection to reduce the crazing: the middle-speed injection filling channel → slowly filling the gate → rapid injection → low-pressure slow to fill the mold so that the mold gas in each paragraph in time to remove clean.
(6) When the screw pre-plastic pressure is too low, the speed is too high, so that the screw back too fast, the air easily with the material together to the front of the barrel.
4, Raw materials:
(1) Raw materials mixed with heterogeneous plastic or aggregates mixed with a large number, easy to entrain air-melted, sometimes silver. Raw materials are susceptible to thermal decomposition when contaminated or contain hazardous scraps.
(2) Recycled material loose structure, the amount of air stored in the large pores; Regeneration of renewable materials too much or a too-high proportion of the new material (generally less than 20%)
(3) Raw materials containing volatile solvents or raw materials in the liquid additives such as white dye auxiliary agent, lubricant silicone oil, plasticizer dibutyl ester, and stabilizers, antistatic agents such as excessive or mixed uneven to Accumulation state into the cavity, the formation of silver grain.
(4) Plastic is not dry or from the atmosphere to absorb moisture. The raw material should be sufficiently dried and the drying hopper should be used.
(5) Some grades of plastic, themselves can not withstand higher temperatures or longer heating time. In particular, when a trace amount of water is contained, a catalytic cracking reaction may occur. For this type of plastic consider adding external lubricants such as stearic acid and its salts (per 10kg material can be added to 50g), in order to reduce its processing temperature.
5, Product design:
Thick wall thickness, and table cooling rate is different. In the mold, manufacturing should be appropriate to increase the size of the main channel, shunt, and gate.
Common problems of plastic processing in addition to blooming, but also shrinkage.