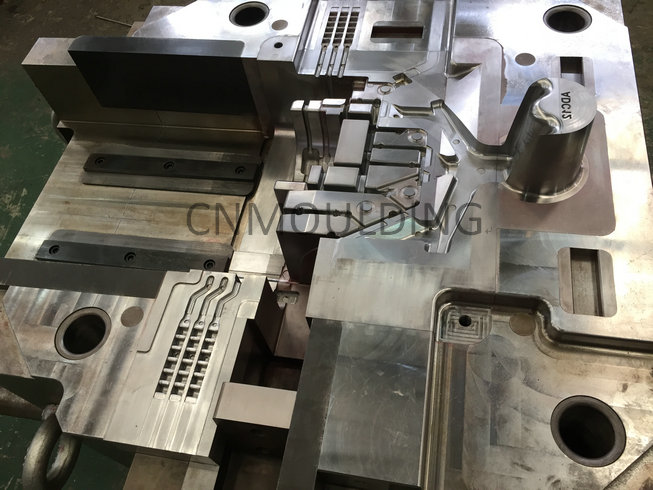
The service life of the Die-casting mold and Die-casting mold material is closely related. Die-casting mold zero, the components are mainly divided into contact with the metal parts, sliding parts and mold parts with structural parts. Die-casting mold cavity and runner and other components in the metal pressure casting production process, directly with the high temperature, high pressure, high-speed metal liquid contact. On the one hand by the metal liquid direct erosion, wear high-temperature oxidation and corrosion. On the other hand, due to the high efficiency of the production, the mold temperature rise and decrease are very severe, and the formation of periodic changes. Therefore, the Die casting mold working environment is very bad. Therefore, attention should be paid to the selection of the material for manufacturing the Die casting mold.
① A good malleability and machinability.
② High temperature red high hardness, high-temperature strength, anti-tempering stability and impact toughness.
③ Has good thermal conductivity and fatigue resistance.
④ Have enough high-temperature oxidation resistance.
⑤ Small thermal expansion coefficient.
⑥ High wear resistance and corrosion resistance.
⑦ Has good hardenability and a smaller heat treatment deformation rate.
Selection of die-casting materials should be based on product performance, process performance, production conditions, economy and the characteristics of Die-casting materials and other factors, a reasonable choice of the right die-casting material. Commonly used mechanical parts Die-casting materials include aluminum alloy, zinc alloy, and magnesium alloy.
Aluminum alloys: These are the most commonly used die casting materials due to their lightweight, high strength, and corrosion resistance. They are often used in the automotive, aerospace, and electronics industries.
Zinc alloys: These are also commonly used in die casting due to their low melting point, high ductility, and good surface finish. They are often used in the production of small parts such as gears, hinges, and locks.
Magnesium alloys: These are lightweight and have excellent strength-to-weight ratios, making them ideal for applications that require high strength and low weight. They are often used in the production of automotive and aerospace components.
Copper alloys: These are used in die casting for their high conductivity and excellent thermal properties. They are often used in the production of electrical components such as connectors and switches.